

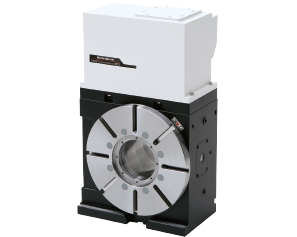
The RollerDrive CNC RCD Series is a circular table designed to meet the requirements of machine tool manufacturers for greater speed and accuracy. The RCD Series uses Sankyo's zero-backlash reducer, the RollerDrive to deliver output motion unaffected by external disturbances, unlike gearmotors or torque motors.
The high accuracy and rigidity afforded by the zero-backlash technology gives the RCD Series its high rotary positioning accuracy 10 seconds maximum, and the ability to hold up to heavy cutting of hard steel.
The high accuracy and rigidity afforded by the zero-backlash technology gives the RCD Series its high rotary positioning accuracy 10 seconds maximum, and the ability to hold up to heavy cutting of hard steel.
RCD Series:
Motor top surface mounting type
(5 models)
Motor top surface mounting type
(5 models)
| RCD170 | RCD200 | RCD250 | RCD300 |
| RCD400 |
| RCD400 |

Permanent accuracy
By adopting our roller drive mechanism, there is no deterioration in the internal parts of the RCD Circular Table and its accuracy does not deteriorate after long-term use. It has excellent durability.
No routine calibration or adjustment work is required.
No routine calibration or adjustment work is required.
Excellent performance characteristics due to the zero-backlash design
With our roller drive mechanism, it is possible for repeated output operations to be equally precise, without being disturbed by external forces. Because it achieves high-precision positioning with a rotational accuracy of 10 seconds or better, it can also be used for heavy cutting on hard steel.
No clamp operation
Since the roller drive CNC has zero play due to its design, it does not require any clamping operations.
With this design, clamping and unclamping time is effectively eliminated and no other energy source is need, unlike conventional hydraulic systems.
With this design, clamping and unclamping time is effectively eliminated and no other energy source is need, unlike conventional hydraulic systems.
No Maintenance and Excellent Price Performance
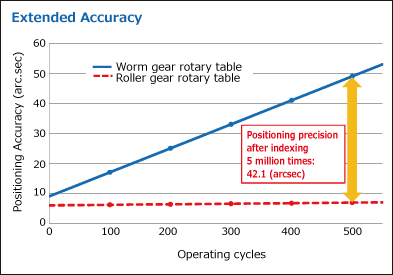
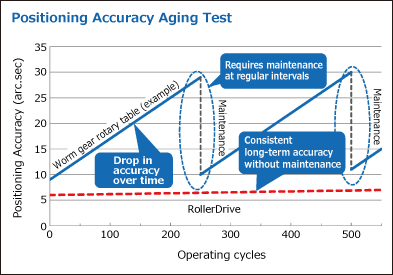
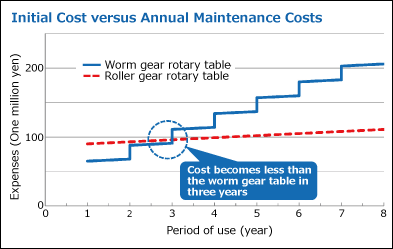
Since the torque is transmitted by rolling contact, the internal mechanism does not wear and the positioning table always maintains its initial level of accuracy, even after long-term use.
<Operating conditions>
Table size: Output table diameter; 170mm
Load inertia: 0.5kg・m2
Indexing angle: 36 ° (1 direction indexing)
Indexing time: 0.35sec
*The roller drive results in the graph on the left are the measured values from our dynamic operating test.
(Both cases used testing machines with the same table diameter)
<Operating conditions>
Table size: Output table diameter; 170mm
Load inertia: 0.5kg・m2
Indexing angle: 36 ° (1 direction indexing)
Indexing time: 0.35sec
<Accuracy after 5 million indexing operations>
Item | Worm gear | RollerDrive |
Variation in accuracy | 42.1sec (assuming there is no maintenance) |
0.9sec |
Backlash | 18μm | 0 |
(Both cases used testing machines with the same table diameter)
With the roller drive CNC, the variation of accuracy due to aging is extremely small, so routine maintenance costs are significantly reduced.
The graph is based on the following conditions:
・Worm gear circular tables require maintenance work twice a year.
・Both cases assume the annu al maintenance costs
(oil changes, and such.) are 3%.
*Both cases are for the same diameter table.
The graph is based on the following conditions:
・Worm gear circular tables require maintenance work twice a year.
・Both cases assume the annu al maintenance costs
(oil changes, and such.) are 3%.
*Both cases are for the same diameter table.

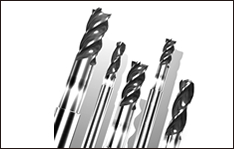
Cutting tool grinding
Higher accuracy by Zero-backlash movement
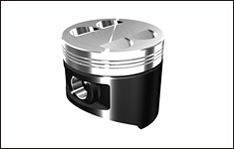
Processing auto parts
High-speed positioning reduces the time spent on non-cutting operations
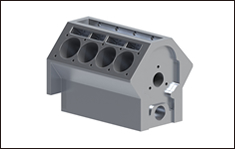
Processing auto parts
High-speed positioning reduces the time spent on non-cutting operations
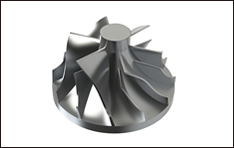
Processing auto parts
5-axis precision, simultaneous, continuous processing
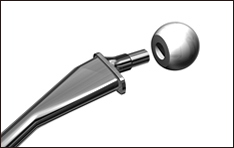
Medical parts
Compact 5 axis
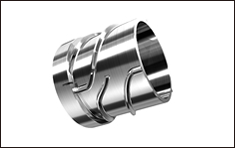
Molding parts
High speed & accurate continuous cutting

RCD Specifications (Motor side surface mounting type)
Characteristics | Units | RCD170 | RCD200 | RCD250 | RCD300 | RCD400 |
Table diameter | mm | φ170 | φ200 | φ250 | φ300 | φ400 |
Table pilot bore diameter | mm | ![]() |
![]() |
![]() |
![]() |
![]() |
Center height | mm | 135 | 135 | 185 | 185 | 230 |
Table T slot width | mm | ![]() |
![]() |
![]() |
![]() |
![]() |
Keyway width | rpm | ![]() |
![]() |
![]() |
![]() |
![]() |
Clamp type (air 0.5 MPa, hydraulic 3.5 MPa) |
Air / Hydraulic | Air / Hydraulic | Hydraulic | Hydraulic | Hydraulic | |
Clamp torque*1 | N·m | 310 | 310 | 1100 | 1100 | 1850 |
Motor shaft equivalent inertia*2,*3 | ×10-4 kg·m2 | 2.96 | 3.15 | 5.70 | 5.70 | 25.76 |
Motor model (FANUC) | α iS8/4000-B (A06B-2215-B400) |
α iS8/4000-B (A06B-2235-B400) |
α iS8/4000-B (A06B-2235-B400) |
α iS8/4000-B (A06B-2235-B400) |
α iS22/4000-B (A06B-2265-B400) |
|
Minimum setting unit | deg | 0.0001 | 0.0001 | 0.0001 | 0.0001 | 0.0001 |
Maximum table speed | min-1 | 70 | 70 | 60 | 60 | 60 |
Gear ratio*2 | 1/50 | 1/50 | 1/60 | 1/60 | 1/60 | |
Indexing accuracy | arc sec | ±15 | ±15 | ±10 | ±10 | ±10 |
Repeatability | arc sec | 8 | 8 | 4 | 4 | 4 |
Net weight | kg | 61 | 69 | 120 | 125 | 291 |
*1 | Values for RCD170, RCD200 are clamping torques when using an air hydro booster with a air pressure of 0.5 MPa as the supply source. |
*2 | The values shown for motor shaft equivalent inertia and continuous/maximum holding torque apply when using a Fanuc motor.Contact Sankyo if using a different motor. |
*3 | Motor shaft equivalent inertia does not include the inertia of the motor shaft. |
*4 | The allowable payload value for upright mounting shown in brackets applies when a tail stock or support table is used. |
*5 | The continuous / maximum holding torque is the allowable load torque when a clamp is not used. |
*6 | Maximum holding torque should not exceed 10 seconds with 20% duty. |
*7 | Simultaneous use of the MP scale (high-accuracy model) and the rotary joint is not supported. |


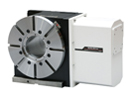
>> RCD Series
Standard model
Motor side surface
mounting type
Motor side surface
mounting type
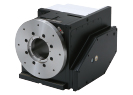
>> RCD Series
Standard model
Motor rear surface
mounting type
Motor rear surface
mounting type