

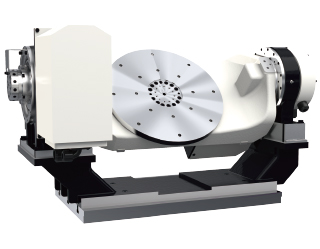
The RTG is a compact, lightweight, tilted rotary table that makes it possible to respond to the increasing number of machining needs of small MCs, the increasing complexity of workpieces, and the increasing size of workpieces.
By using the RTG series equipped with A and C axes you can take advantage of process aggregation, efficient machining postures and tool selection, even when machining workpieces that had previously required multiple processes. In addition, in order to meet the needs of unmanned machines and enjoy the benefits of robots, rotary joints with up to 13 (12 +1) ports are available for automatic installation and removal of workpieces with seating confirmation.
Furthermore, the use of a RollerDrive mechanism eliminates the need for clamping during machining, thus reducing the positioning time by approximately one-third, compared with conventional worm gear rotary tables that use clamps. The RollerDrive mechanism can be operated continuously, with only a short break to change the lubrication oil. It eliminates the need for periodic backlash readjustments like the conventional worm gear rotary tables.
This contributes to significantly reduced equipment maintenance. The RTG is ideal for small MCs, while automating operations and improving productivity.
By using the RTG series equipped with A and C axes you can take advantage of process aggregation, efficient machining postures and tool selection, even when machining workpieces that had previously required multiple processes. In addition, in order to meet the needs of unmanned machines and enjoy the benefits of robots, rotary joints with up to 13 (12 +1) ports are available for automatic installation and removal of workpieces with seating confirmation.
Furthermore, the use of a RollerDrive mechanism eliminates the need for clamping during machining, thus reducing the positioning time by approximately one-third, compared with conventional worm gear rotary tables that use clamps. The RollerDrive mechanism can be operated continuously, with only a short break to change the lubrication oil. It eliminates the need for periodic backlash readjustments like the conventional worm gear rotary tables.
This contributes to significantly reduced equipment maintenance. The RTG is ideal for small MCs, while automating operations and improving productivity.
RTG Series(1 model)
| RTG500 |

・Built-in, no-backlash RollerDrive mechanism
・ Clampless processing drastically increases the ratio of cutting to non-cutting time
・ Lightweight and compact, and can be mounted on the #30 vertical MCs
・ Provides a large jig area of φ 500 x H270
・ Rotary joint is equipped with up to 12 + 1 ports
・ Routine maintenance is just an oil change, nothing else.
・ Clampless processing drastically increases the ratio of cutting to non-cutting time
・ Lightweight and compact, and can be mounted on the #30 vertical MCs
・ Provides a large jig area of φ 500 x H270
・ Rotary joint is equipped with up to 12 + 1 ports
・ Routine maintenance is just an oil change, nothing else.
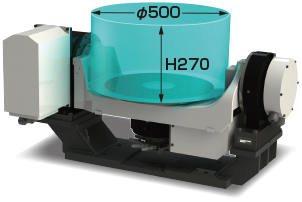

Specifications | RTG500 | |||||
Rotating axis | Tilting axis | |||||
Tilting angle | deg | -30 to +120 | ||||
Table diameter | mm | φ120 | ||||
Table pilot bore diameter*1 | mm | ![]() |
||||
Center height at tilted axis +90° | mm | 350 | ||||
Tabletop height at 0° tilted axis | mm | ![]() |
||||
Guide block width | mm | 1,800 | ||||
Total gear ratio | 1/72 | 1/72 | ||||
Motor shaft equivalent inertia*1 *2 *3 | ×10−4kg・m2 | 1.41 (1.43) | 6.22 (6.97) | |||
Motor used (FANUC ・ BROTHER) | αiF4/5000-B (A06B-2223-B300) |
R2AAB8100F~ | αiS8/4000-B (A06B-2235-B300) |
R2AA13180H~ | ||
Maximum table rotational speed | min-1 | 69 | 55 | 48 | ||
Indexing accuracy | arc sec | ±15 | ±30 | |||
Repeatability | arc sec | 8 | 8 | |||
Net weight | kg | 248 | ||||
Net weight(when joints are rotary joint is installed) | kg | 270 | ||||
Allowable payload | kg | 100 | ||||
Maximum jig work diameter | mm | 500 | ||||
Allowable workpiece inertia | kg・m2 | 2.3 | ||||
Maximum radial load |
![]() |
N | 23000 | |||
Allowable continuous holding torque |
![]() |
N・m | 259 | 254 | − | − |
Allowable maximum holding torque*4 |
N・m | 415 | 318 | − | − | |
Allowable continuous holding torque |
![]() |
N・m | − | − | 518 | 648 |
Allowable maximum holding torque*4 |
N・m | − | − | 835 | 713 | |
Internal eccentric load torque*5 |
![]() |
N・m | 0 | 112 | ||
Lubrication method | Oil bath (and grease for the support unit) | |||||
Oil type/quantity | Mobile SHC629 / 0.7L | Mobile SHC629 / 1.4L | ||||
Rotary joint (number of ports) | 12+1 |
*1 Values when a rotary joint is not installed.
*2 Values in parentheses ( ) are when a rotary joint is installed
*3 The specified motor shaft equivalent inertia does not include the inertia of the motor shaft.
*4 Maximum holding torque shall be a maximum of 30 seconds at a 40% duty cycle.
*5 This is the value of the unbalanced torque of the rotating shaft acting on the tilt axis at a tilt angle of +90°.(0.112 m x 102 kg x 9.8)
*2 Values in parentheses ( ) are when a rotary joint is installed
*3 The specified motor shaft equivalent inertia does not include the inertia of the motor shaft.
*4 Maximum holding torque shall be a maximum of 30 seconds at a 40% duty cycle.
*5 This is the value of the unbalanced torque of the rotating shaft acting on the tilt axis at a tilt angle of +90°.(0.112 m x 102 kg x 9.8)


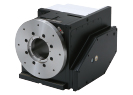
>> RCD Series
Standard model
Motor rear surface
mounting type
Motor rear surface
mounting type
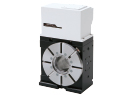
>> RCD Series
Standard model
Motor top surface
mounting type
Motor top surface
mounting type