

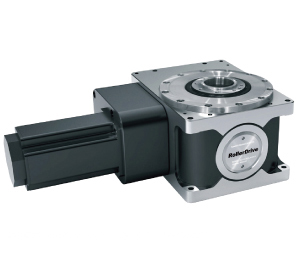
RU80〔High Gear Ratio Model〕
With the RollerDrive RU Series, a servomotor is mechanically reduced while maintaining powerful torque, rigidity and stability. An output motion faithful to input control commands can be attained by achieving zero-backlash with our unique preloaded mechanism. This is a revolutionary FA motion control unit, which combines rolling transmission for high-efficiency and elimination of wear, an orthogonal layout of input and output axes for greater compactness, and standard features like a large diameter hollow shaft for greater ease-of-use.
RU Series(5 models)
| RU40 | RU63 | RU80 | RU100 | RU125 |
RU Series Large Model(6 models)
| RU160 | RU200 | RU250 | RU315 |
| RU400 | RU500 |
| RU400 | RU500 |

Heavy-duty drive with a compact motor
Our product lineup includes high gear ratio reducers that use proprietary reducer gears to deliver heavy torque using a small servomotor. Gear ratios are 1/20, 1/60 (RU40 comes with 1/15 or 1/45)
High rigidity
The internal structure was redesigned with a cast ironhousing and heavy-duty output bearing for high rigidity.
Flexible Servomotor Options
Compatible with a wide range of servomotor sizes (for each brand).
Servomotors are coupling-mounted for installation. Easy to install even for first-time users.
Servomotors are coupling-mounted for installation. Easy to install even for first-time users.
Suitable for Use in Harsh Environments
We offer a water-proof and dust-proof option that uses a special seal for protection against washdown and
dust-prone environments.


RU40 to RU125 Capacity Table[Grease Lubrication]
Size | RU40 | RU63 | RU80 | RU100 | RU125 | |||||||
Gear ratio | 15 | 45 | 20 | 60 | 20 | 60 | 20 | 60 | 20 | 60 | ||
Max Acceleration Torque start/stop | N・m | 67 | 155 | 211 | 647 | 1,098 | ||||||
Static rated output torque | N・m | 100 | 250 | 360 | 1,000 | 1,800 | ||||||
Maximum output speed* | min-1 | 200 | 150 | 125 | 100 | 80 | ||||||
Rated output speed* | min-1 | 60 | 40 | 35 | 30 | 30 | ||||||
Internal moment of inertia at the input shaft | ×10-4kg・m2 | 0.53 | 0.15 | 1.85 | 0.53 | 5.05 | 1.94 | 9.51 | 5.45 | 32.99 | 13.51 | |
Angular transmission accuracy |
Standard accuracy model |
arc sec or less |
90 | 60 | 40 | |||||||
High accuracy model |
- | 30 | 20 | |||||||||
Angular repeatability accuracy |
Standard accuracy model |
arc sec or less |
±10 | ±7 | ±5 | |||||||
High accuracy model |
- | ±3 | ±2 | |||||||||
Output shaft axial runout (Side V) |
Standard accuracy model |
μm or less | 10 | |||||||||
High accuracy model |
- | 2 | ||||||||||
Output shaft radial runout (Side V) |
Standard accuracy model |
μm or less | 10 | |||||||||
High accuracy model |
- | 2 | ||||||||||
Allowable axial load output shaft | N | 3,000 | 12,500 | 16,500 | 21,000 | 50,000 | ||||||
Allowable radial load output shaft | N | 2,000 | 11,000 | 14,000 | 18,000 | 35,000 | ||||||
Allowable moment load output shaft | N・m | 100 | 700 | 1,000 | 1,700 | 5,000 | ||||||
Weight | kg | 9 | 10 | 20 | 22 | 35 | 40 | 50 | 55 | 95 | 100 |
RU40 to RU125 Capacity Table[Oil Lubrication]
Size | RU40 | RU63 | RU80 | RU100 | RU125 | |||||||
Gear ratio | 15 | 45 | 20 | 60 | 20 | 60 | 20 | 60 | 20 | 60 | ||
Max Acceleration Torque start/stop | N・m | 82 | 191 | 260 | 796 | 1,352 | ||||||
Static rated output torque | N・m | 100 | 250 | 360 | 1,000 | 1,800 | ||||||
Maximum output speed* | min-1 | 200 | 150 | 150 | 150 | 150 | ||||||
Rated output speed* | min-1 | 86 | 55 | 50 | 45 | 45 | ||||||
Internal moment of inertia at the input shaft | ×10-4kg・m2 | 0.53 | 0.15 | 1.85 | 0.53 | 5.05 | 1.94 | 9.51 | 5.45 | 32.99 | 13.51 | |
Angular transmission accuracy |
Standard accuracy model |
arc sec or less |
90 | 60 | 40 | |||||||
High accuracy model |
- | 30 | 20 | |||||||||
Angular repeatability accuracy |
Standard accuracy model |
arc sec or less |
±10 | ±7 | ±5 | |||||||
High accuracy model | - | ±3 | ±2 | |||||||||
Output shaft axial runout (Side V) |
Standard accuracy model |
μm or less | 10 | |||||||||
High accuracy model |
- | 2 | ||||||||||
Output shaft radial runout (Side V) |
Standard accuracy model |
μm or less | 10 | |||||||||
High accuracy model |
- | 2 | ||||||||||
Allowable axial load output shaft | N | 3,000 | 12,500 | 16,500 | 21,000 | 50,000 | ||||||
Allowable radial load output shaft | N | 2,000 | 11,000 | 14,000 | 18,000 | 35,000 | ||||||
Allowable moment load output shaft | N・m | 100 | 700 | 1,000 | 1,700 | 5,000 | ||||||
Weight | kg | 9 | 10 | 20 | 22 | 35 | 40 | 50 | 55 | 95 | 100 |
Large Model
Size | RU160 | RU200 | RU250 | RU315 | RU400 | RU500 | ||||||||
Gear ratio | 24 | 72 | 30 | 90 | 30 | 100 | 32 | 120 | 36 | 120 | 40 | 150 | ||
Max Acceleration Torque start/stop | N・m | 1,730 (1,410) | 2,170 (1,760) | 6,250 | 8,710 | 15,530 | 26,090 | |||||||
Static rated output torque | N・m | 2,400 | 3,090 | 8,140 | 11,720 | 21,290 | 34,950 | |||||||
Maximum output speed*1 | min-1 | 100 (60) | 65 (40) | 40 | 30 | 25 | 20 | |||||||
Rated output speed*1 | min-1 | 30 (25) | 25 (20) | 20 | 15 | 13 | 12 | |||||||
Internal moment of inertia at the input shaft*2 |
×10-2 kg ・m2 |
0.57 (0.41) |
0.26 | 0.68 (0.52) |
0.36 | 3.44 (3.28) |
0.71 | (6.97) | 1.27 | (20.56) | 2.94 | (28.91) | 3.55 | |
Angular transmission accuracy |
Standard accuracy model |
arc sec or less |
40 | |||||||||||
High accuracy model |
20 | |||||||||||||
Angular repeatability accuracy |
Standard accuracy model | arc sec or less |
±5 | |||||||||||
High accuracy model |
±3 | |||||||||||||
Output shaft axial runout (Side V) |
Standard accuracy model | μm or less |
10 | |||||||||||
High accuracy model |
3 | 5 | ||||||||||||
Output shaft radial runout (Side V) |
Standard accuracy model | 10 | ||||||||||||
High accuracy model |
3 | 5 | ||||||||||||
Allowable axial load output shaft | N | 55,000 | 63,000 | 130,000 | 140,000 | 160,000 | 180,000 | |||||||
Allowable radial load output shaft | N | 43,000 | 48,000 | 95,000 | 110,000 | 135,000 | 150,000 | |||||||
Allowable moment load output shaft | N・m | 9,700 | 16,000 | 38,000 | 65,000 | 110,000 | 200,000 | |||||||
Weight | kg | 140 | 155 | 180 | 200 | 380 | 425 | 660 | 705 | 985 | 1,066 | 1,585 | 1,715 |
*1 Avoid using in situations that result in output with continuous rotation at 360 degrees or more.
*2 Figures in brackets [ ] are for standard gear ratio models without the attachment.
*2 Figures in brackets [ ] are for standard gear ratio models without the attachment.

